Challenges in Vibration Isolation System Implementation
Common but Overlooked Challenges in Vibration Isolation System Implementation—and How to Solve Them
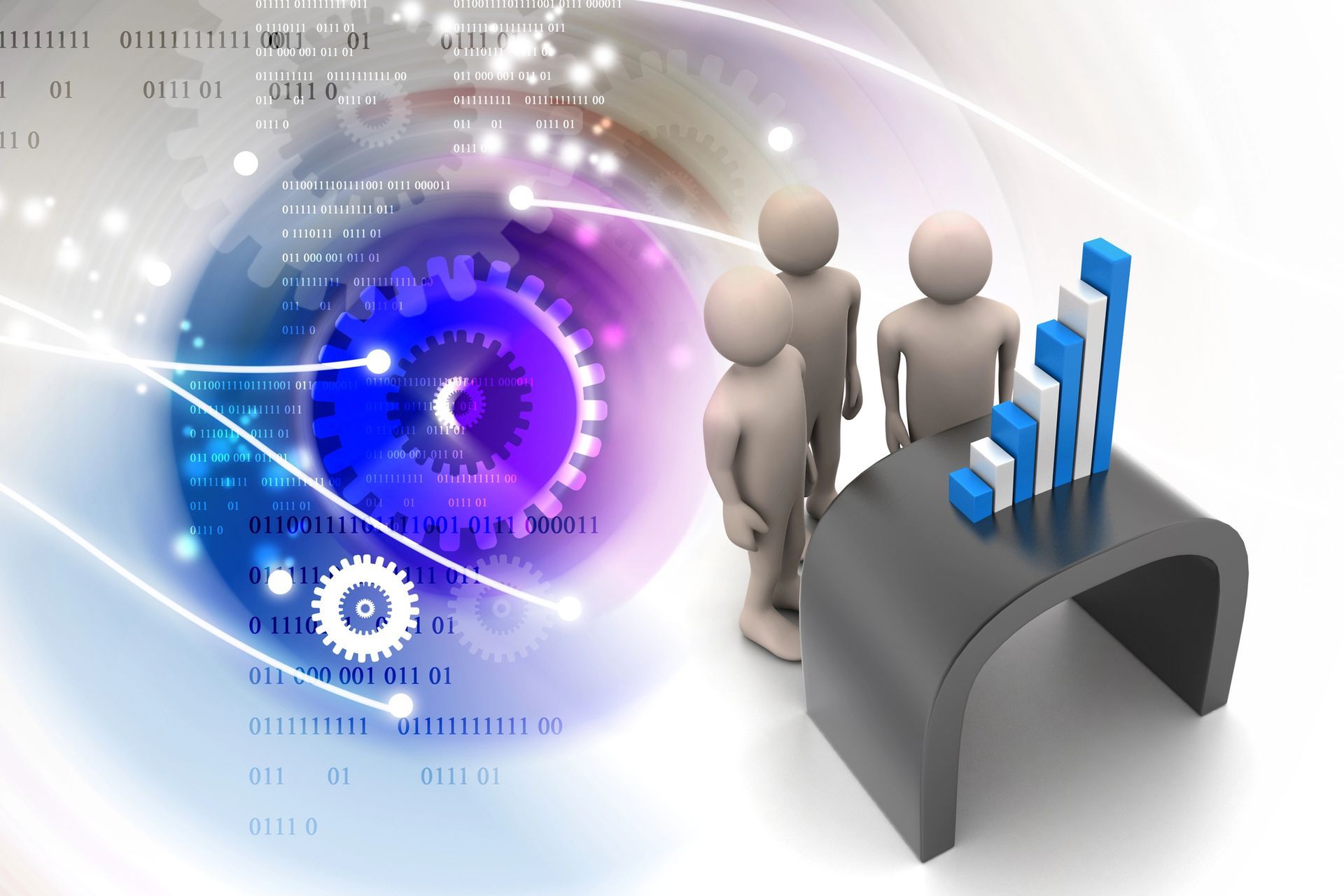
Vibration isolation systems are essential for protecting sensitive equipment in laboratories, manufacturing plants, and high-tech facilities. While dramatic failures make headlines, most real-world issues are subtle: small design oversights, improper installation, and overlooked maintenance. These minor missteps can quietly undermine the performance of vibration isolation systems, leading to reduced equipment life, product defects, and costly downtime. This article explores the most prevalent, yet less obvious, challenges in vibration isolation—and provides actionable solutions for each.
Improper Design and Specification
One of the most common sources of trouble is inadequate design and specification. Often, the vibration environment is not fully assessed before choosing an isolation solution. For example, failing to account for the frequency and amplitude of vibrations, or neglecting to consider the direction (horizontal vs. vertical), can lead to using the wrong type or size of isolator. Sometimes, design teams overlook the impact of attached piping or electrical connections, which can inadvertently “short-circuit” the isolation system by providing rigid paths for vibration to bypass the isolators.
Solution:
- Conduct a thorough vibration survey and analysis before specifying any isolation products.
- Use simulation tools or consult standards (like the ASHRAE Handbook) to ensure the selected isolators match the vibration profile of the environment.
- Consider all load paths, including attached utilities, and ensure they are properly decoupled.
Incorrect Isolator Selection
Selecting an isolator based solely on weight or catalog specs is a common mistake. The natural frequency of the isolator should be well below the dominant vibration frequencies in the environment. If not, the isolator may amplify rather than reduce vibrations. For instance, using a rigid pad or a spring with insufficient static deflection results in a high natural frequency and poor isolation at critical frequencies.
Solution:
- Choose isolators with enough static deflection to achieve a low natural frequency, ideally less than one-third of the lowest disturbing frequency.
- Consult with manufacturers or vibration experts, and request performance data for your specific application.
- Factor in environmental conditions such as temperature, humidity, and potential chemical exposure.
Installation Errors
Even the best-designed systems can be compromised by poor installation practices. Common errors include misalignment of springs, forgotten shims, or placing rigid supports (like bolts or pipes) in parallel with the isolator. These mistakes can create unintended load paths, increasing system stiffness and reducing isolation efficiency. For example, if a metal bolt makes contact between the equipment and the floor, it can transmit vibrations directly, negating the benefit of the isolators.
Solution:
- Follow manufacturer installation instructions carefully, ensuring all surfaces are clean and level before mounting isolators.
- Use flexible connectors for all piping and electrical connections to avoid rigid links.
- After installation, test the system and make adjustments as needed to ensure optimal performance.
Inadequate Maintenance
Vibration isolation systems are often installed and then forgotten. Over time, components can corrode, settle, or become misaligned, especially in older facilities. Neglected hardware may continue to support equipment, but its isolation effectiveness can be severely diminished. Regular inspections are rare, and maintenance is often reactive rather than proactive.
Solution:
- Establish a regular inspection and maintenance schedule for all isolation hardware.
- Replace or repair corroded, worn, or damaged components promptly.
- Monitor vibration levels periodically to detect performance degradation early.
Adjustment and Load Changes
Some vibration isolation systems require manual adjustment to compensate for changes in equipment weight, distribution, or environmental conditions. If these adjustments are not made, the system may become unbalanced or ineffective. For example, adding new equipment or changing the layout without recalibrating the isolators can lead to uneven load sharing and reduced isolation.
Solution:
- Use isolators that allow for easy adjustment, or consider active systems that can self-compensate for changes in load.
- Whenever equipment is added, moved, or modified, reassess and, if necessary, rebalance the isolation system.
Space and Integration Constraints
In many facilities, space for isolation systems is limited. The system must fit within the available footprint and sometimes inside machine housings or vacuum chambers. Poor planning can result in isolators that are too large or too small for the application, or that interfere with other systems.
Solution:
- Measure available space carefully and select isolators that fit both physically and functionally.
- For unique environments, such as vacuum chambers, consider specialized solutions like negative-stiffness isolators that require no air or electricity and can be customized for tight spaces.
While catastrophic vibration isolation failures are rare, small and often overlooked mistakes are common—and can have a significant impact on sensitive operations. By paying attention to proper design, selection, installation, maintenance, adjustment, and integration, facility managers and engineers can ensure their vibration isolation systems deliver reliable, long-term performance.
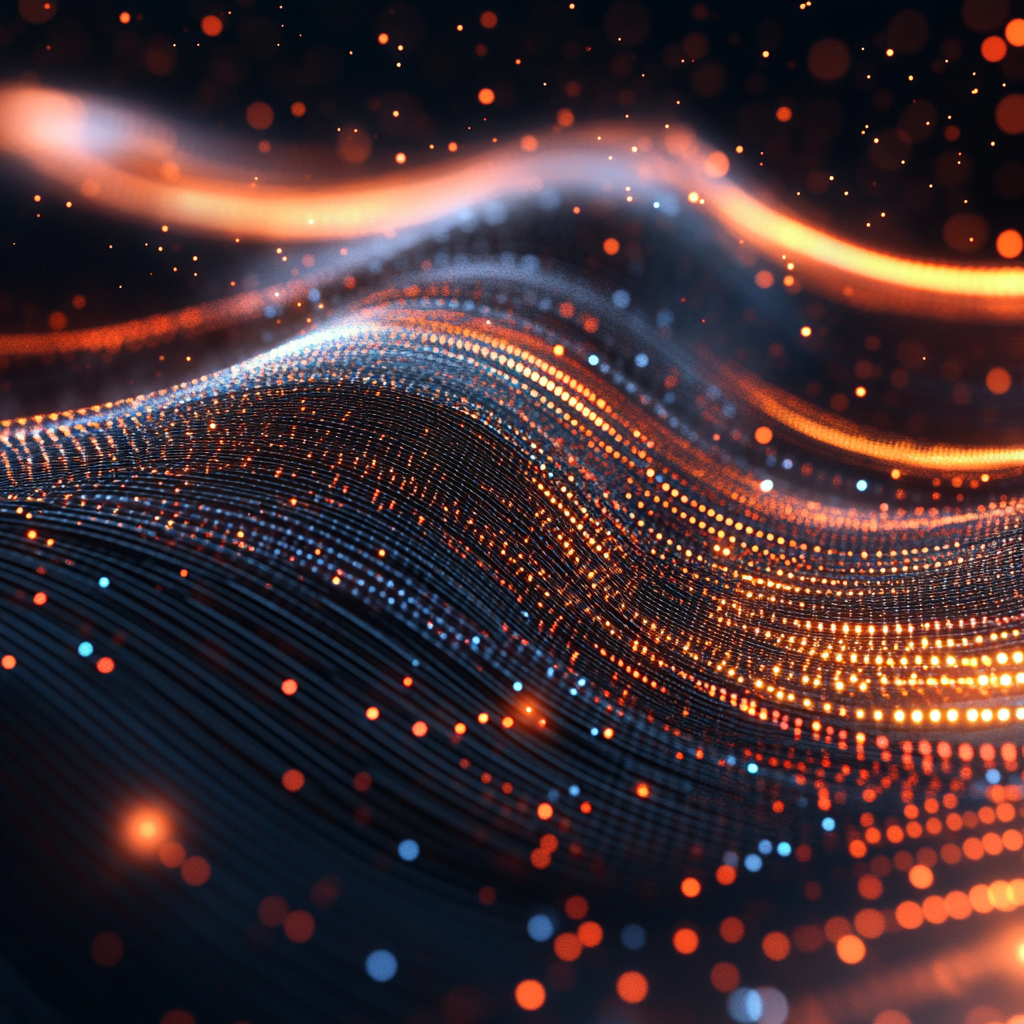
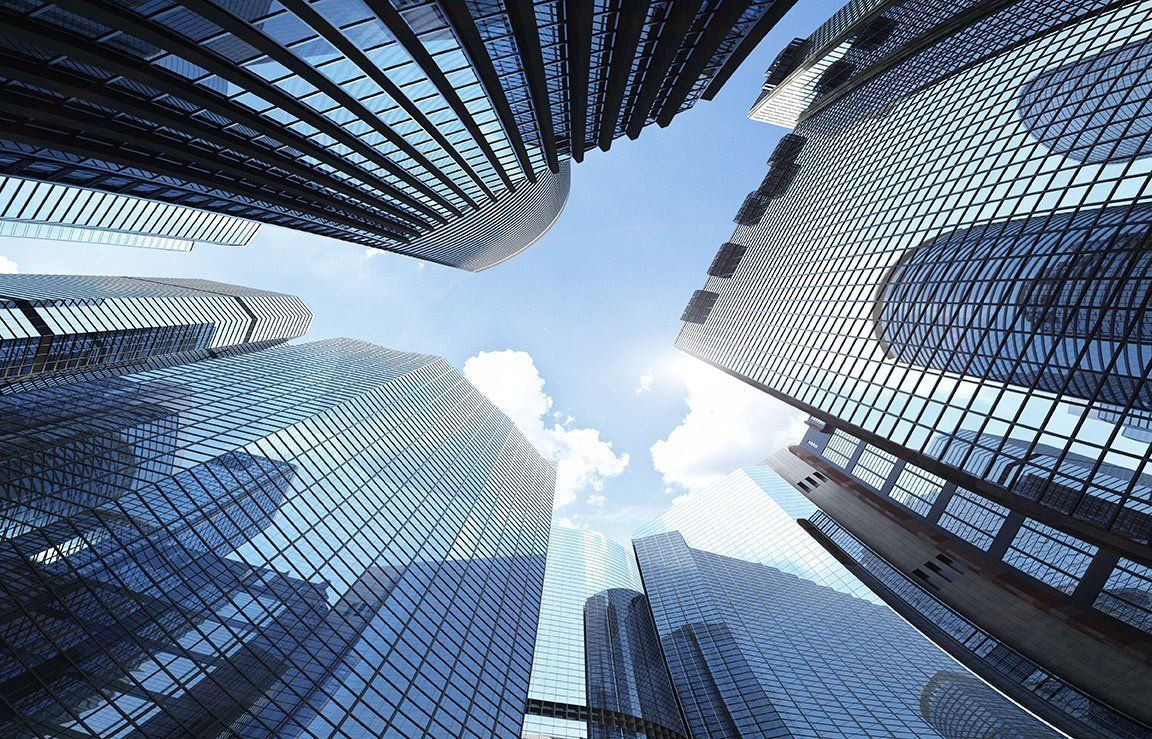