Silent Saboteurs
Design Flaws Undermine Vibration Isolation—and the Tech Fixing It
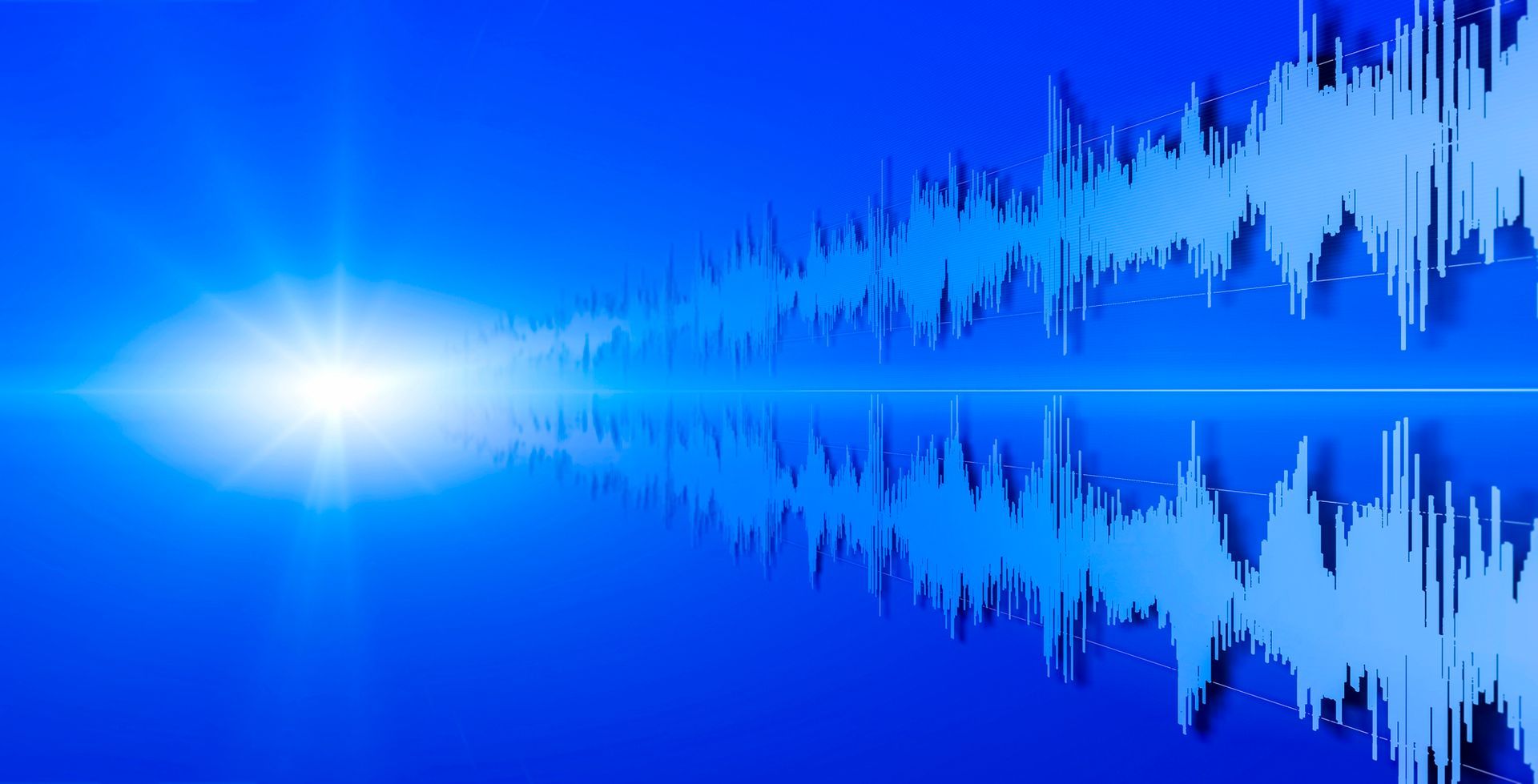
In the high-stakes worlds of semiconductor manufacturing, quantum research, and precision medicine, even the tiniest vibrations can spell disaster. A misaligned lithography pattern, a blurred electron microscope image, or a failed embryo implantation might trace back to a silent culprit: flawed vibration isolation design. This article explores how seemingly minor design errors lead to major losses—and how cutting-edge solutions like ARIS MD are rewriting the rules.
The Hidden Flaws in Vibration Isolation Design
1. The Short-Circuit Effect
Imagine installing shock absorbers on a car, then bolting the chassis directly to the axle. That’s essentially what happens when vibration isolators are "shorted" by rigid connections like pipes, bolts, or misaligned bases.
- Real-World Example: A semiconductor fab in Tel Aviv installed passive elastomeric isolators to dampen subway vibrations. But rigid piping and uneven bases created direct vibration paths, amplifying resonance by 300% and causing a 0.3% yield drop ($3.6M/year).
2. The Frequency Mismatch
Isolators must have a natural frequency (fₙ) far below the vibration source’s frequency (f). Yet many systems use stiff springs or pads with high fₙ, rendering them useless against low-frequency vibrations (e.g., HVAC systems, urban traffic).
- Data Insight: A spring with fₙ = 12 Hz amplifies subway vibrations (12–15 Hz). Efficiency plummets to -8 dB (worse than no isolation).
3. The Installation Trap
Even perfect designs fail if installed incorrectly. Common errors include:
- Forgotten shims creating unintended load paths.
- Rigid anchors parallel to isolators (e.g., over-tightened bolts).
- Undersized bases forcing equipment to rest on structural elements.
Case Study: When Good Intentions Fail
The $12M Lab That Couldn’t
A microelectronics lab near a subway line invested in passive isolation for its EUV lithography tools. Despite meticulous planning, persistent defects emerged.
Root Causes:
- Design: Isolators (12 Hz fₙ) resonated with subway vibrations.
- Installation: Pipes rigidly connected to the floor bypassed isolators.
- Environment: No inertia bases to counteract rocking motions.
Outcome:
- Yield dropped to 94.2% (0.3% loss = $3.6M/year).
- Downtime costs hit $18k/hour.
The ARIS MD Revolution
How It Works
ARIS MD, developed by K&S Advanced Systems, replaces passive “dumb” isolators with AI-driven active systems:
- Active Control: Generates counter-vibrations in real-time (0.5–100 Hz range).
- Modular Design: Units slot under equipment without foundation changes.
- Six-Axis Isolation: Neutralizes vibrations in all directions (x, y, z, pitch, roll, yaw).
ARIS MD vs. Traditional Isolators - https://www.kns-systems.com/arismd
Why ARIS MD Solves Old Problems
- Eliminates Resonance: Active control neutralizes low-frequency vibrations (e.g., 0.5 Hz from subway trains).
- Foolproof Installation: Pre-assembled modules avoid “shorting” errors.
- Future-Proof: Software updates improve performance; modules scale for heavier equipment.
Case Study Fix:
FAB retrofitted ARIS MD 500 units under its lithography tools. Yield rebounded to 94.7%, and vibrations met VC-E standards (0.75 µm/s). ROI: 11 months.
The Future of Vibration Control
AI and IoT Integration
ARIS MD’s built-in sensors map vibration patterns, predict disturbances (e.g., construction nearby), and auto-adjust damping. In IVF labs, it even mimics natural fallopian tube vibrations (5 µm/s) to boost embryo success rates.
Sustainability Edge
By eliminating concrete seismic blocks, ARIS MD cuts CO₂ emissions by 40% per installation.
Traditional vibration isolation systems are like using a flip phone in the smartphone era—functional but hopelessly outdated. ARIS MD’s blend of AI, modularity, and active control doesn’t just fix design flaws; it redefines what’s possible in precision industries. For labs and fabs battling invisible vibrations, upgrading isn’t optional - it’s survival.
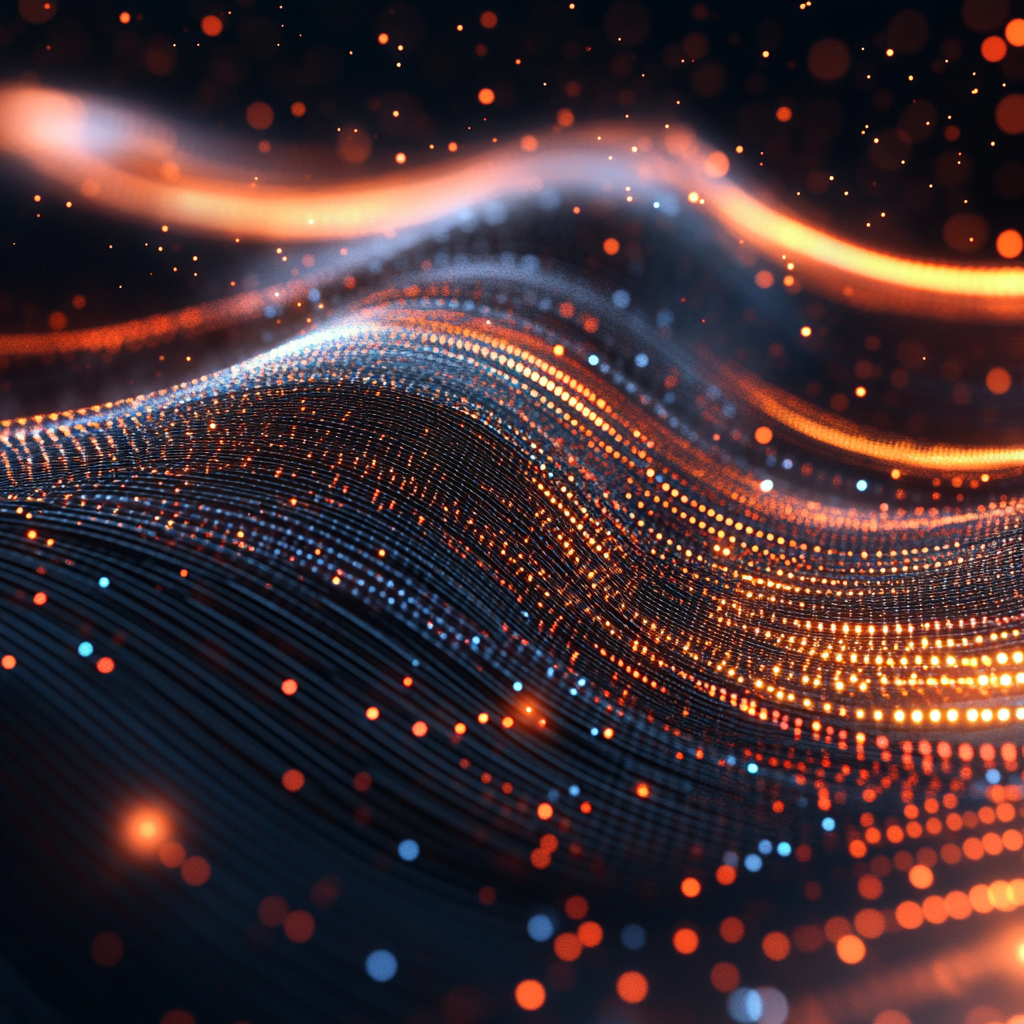
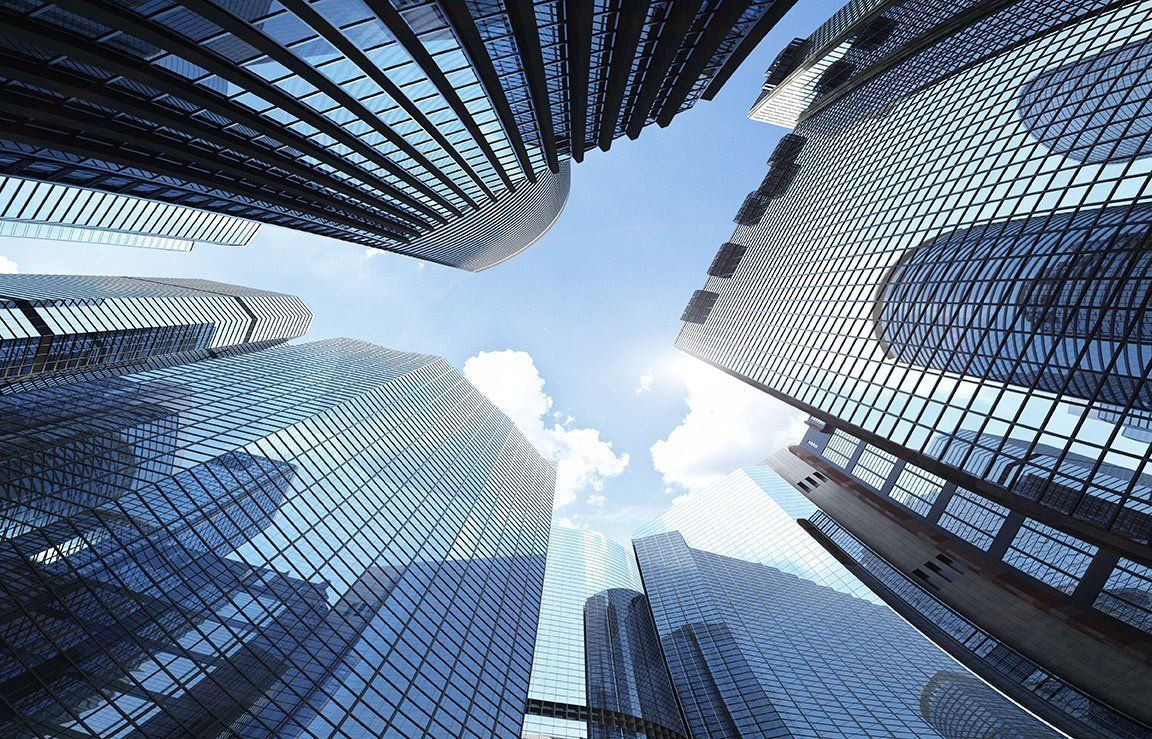